Magic Word: Remote
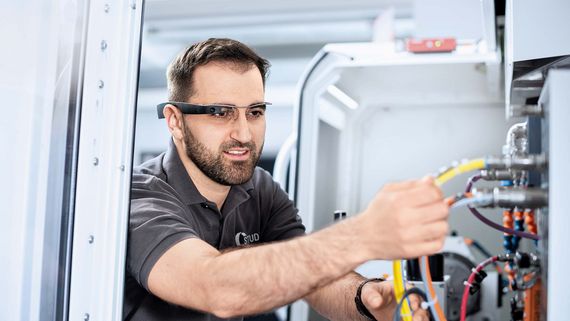
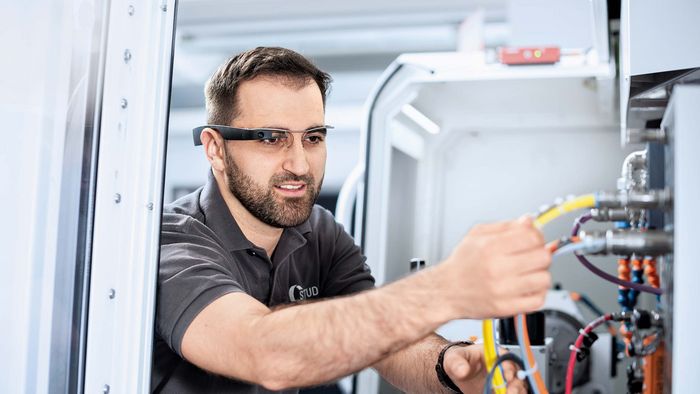
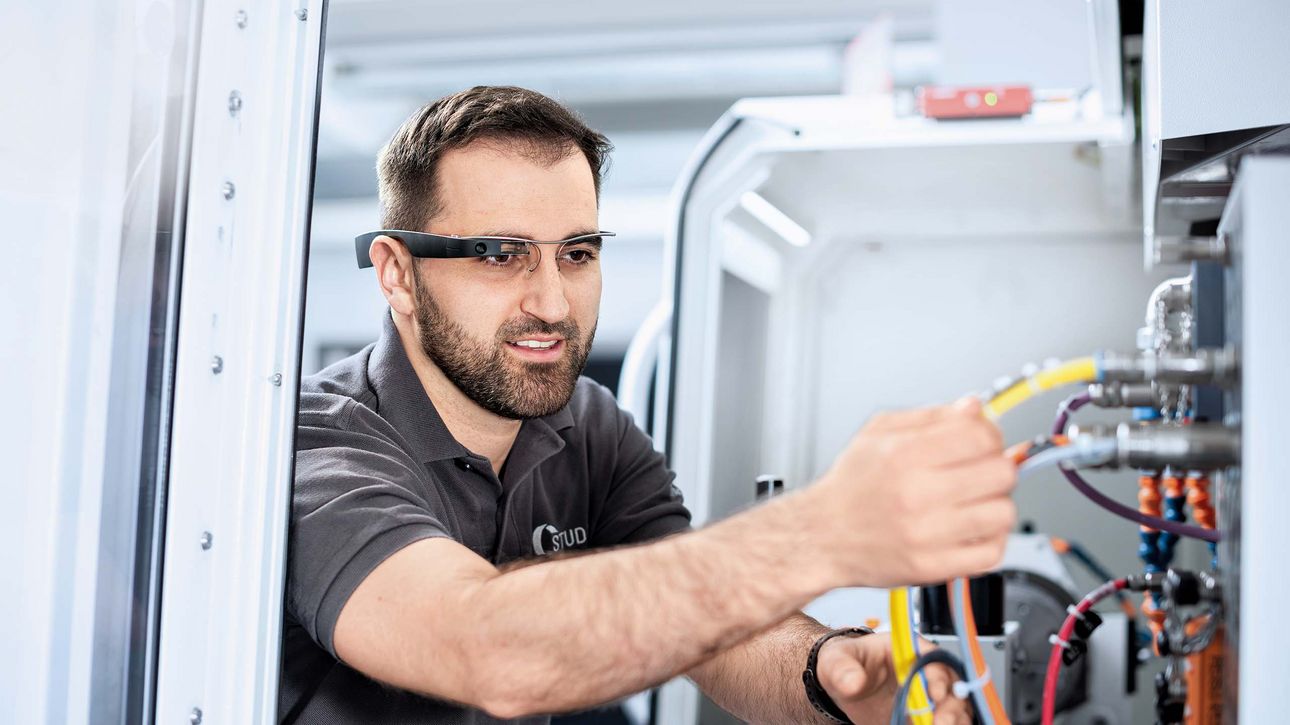
OFTEN IT IS ONLY SMALL OBSTACLES that cause production to come to a halt. A backup battery, for example, which maintains the power supply of a machine control system in the event of a power failure, must be changed from time to time. The machine operator receives a notice on their operating panel in a timely manner. The production manager has already seen this on their production monitor and therefore has replacement batteries already in stock. The user manual and installation instructions are available to both of them in the Customer Cockpit.
If you still need the help of UNITED GRINDING, you can send a service request directly through the Digital Solutions app. The service technician is connected live via the Conference Center integrated in the Customer Cockpit and can provide tips and hints. Images can be sent via the whiteboard function and the helpline technician can draw markers directly into the images. And so the battery is quickly replaced and production can start again.
Save Money and Time
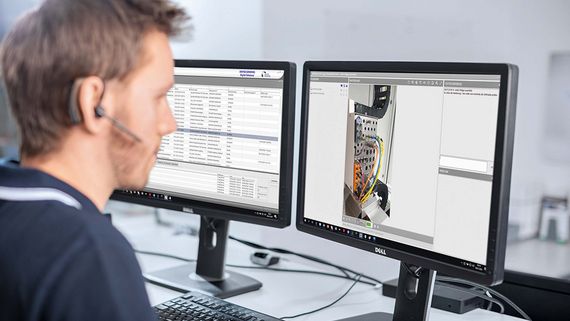
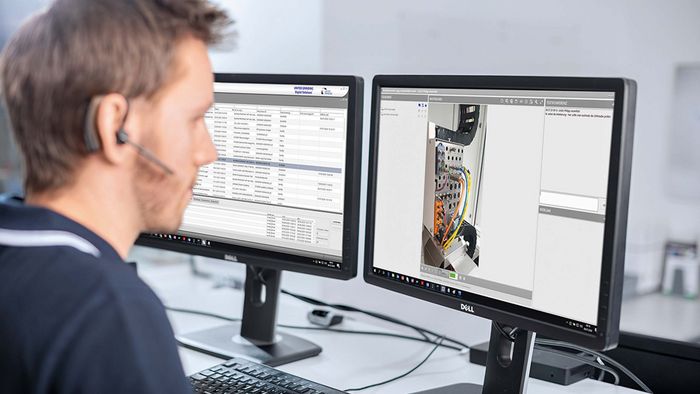
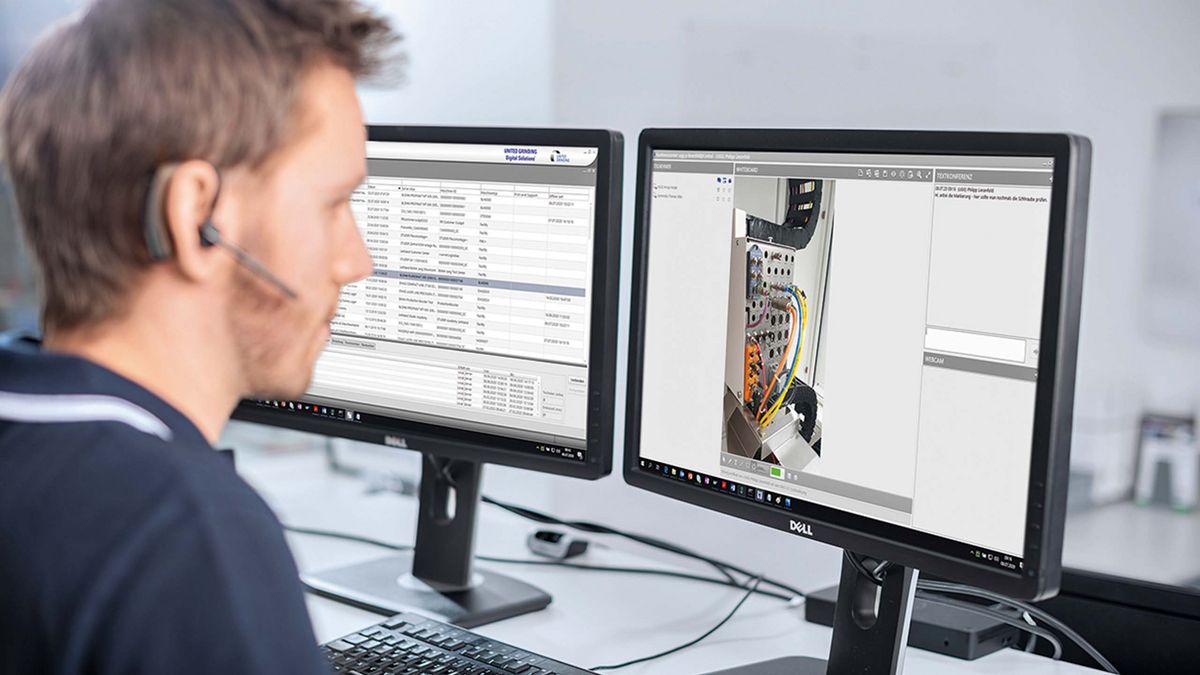
Not only in the times of coronavirus: Not having an appointment for the technician's attendance often saves time and money. If customers can help themselves with problems, it means that operations can usually start up again faster. However, the UNITED GRINDING Group does not leave its customers alone, but supports them with innovative solutions from UNITED GRINDING Digital Solutions™. "Helping our customers increase their productivity with digital solutions is our top priority," explains Chief Technology Officer, Christoph Plüss.
UNITED GRINDING Digital Solutions™ currently offers customers three products: the Production Monitor, the Service Monitor and the Remote Service. The two monitor solutions help customers keep track of their production. When is maintenance work required and what type of maintenance? How does production work, how busy are machines, where may problems arise? This is demonstrated by the service and the production monitor – in real time.
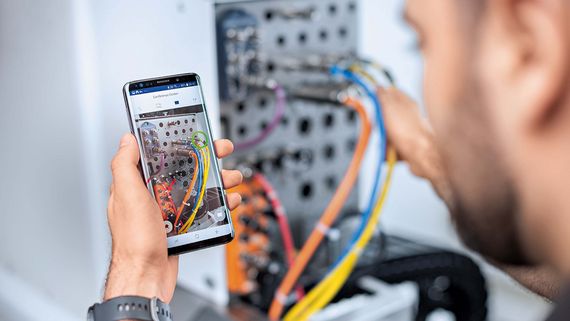
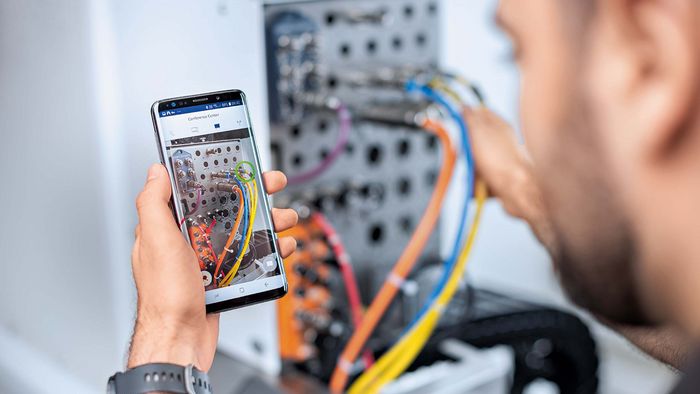
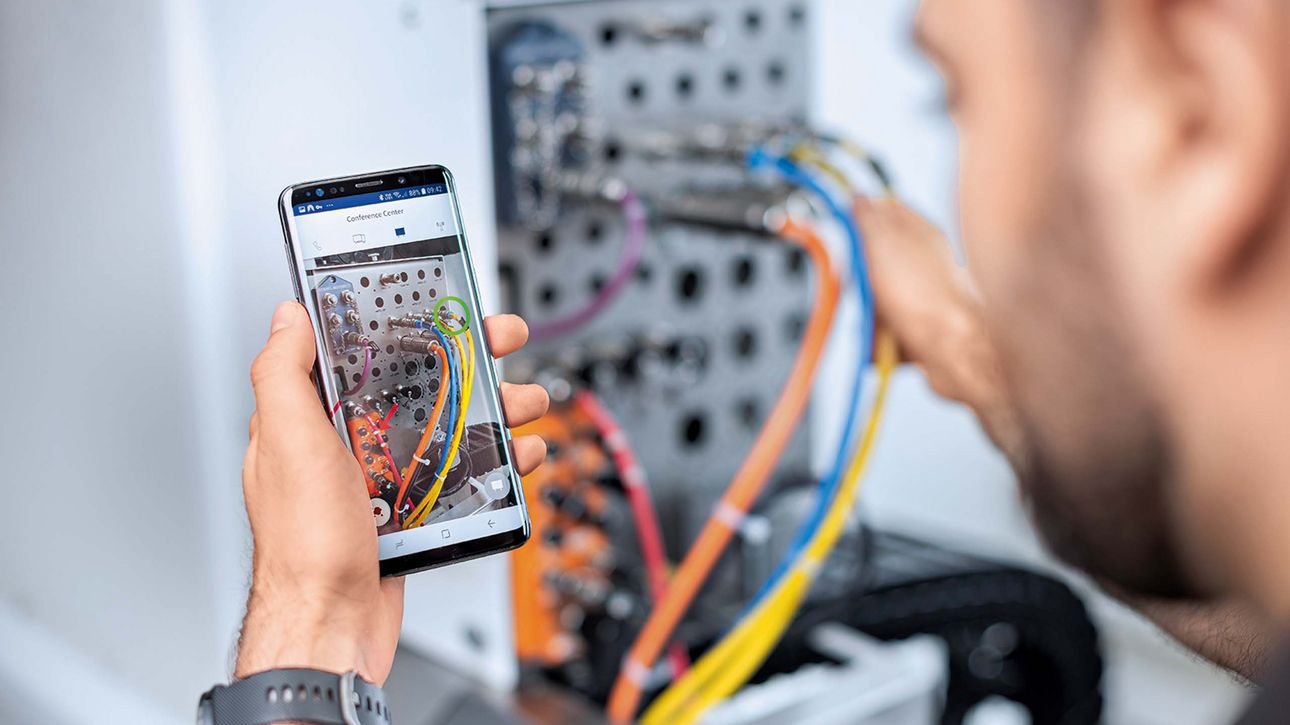
Secure Data Connection
The Remote Service helps to support the UNITED GRINDING help desk over a data connection. Of course, you could always call the help desk. “But technical enquiries on the phone without image support can be very lengthy, as experience has shown,” explains Philipp Liesenfeld, Product Manager Digital Solutions. That’s why the specialists at UNITED GRINDING have integrated the Conference Center into Digital Solutions. The Conference Center app has now been redesigned. “We primarily want to reach customers on the device that everyone always has in their pocket – on their smartphone. And we want to make new apps available to them as easily as possible,” emphasizes Christian Josi, Head of Digital Engineering.
Also, due to the travel restrictions of the coronavirus pandemic, these remote services have been introduced into the daily work of the group of companies and their customers. Remote training was carried out in all brands and the services were immediately used by customers.
Camera in the Machine
"Demand for it particularly increased in the times of coronavirus. During the lockdown, there were 2,500 remote deployments worldwide, more than 1,000 of them taking place in North America. This involved problems that the customer had with the machine or application support," explains Head of Business Development & Marketing, Paul Kössl.
UNITED GRINDING North America also performs customer preliminary acceptances remotely. For this purpose, the application team produces videos of the required processes. "We mount a GoPro camera in the machine to capture the grinding cycle," explains Joseph Szenay, Vice President Customer Care. A time code is used to document the duration of the processing cycle from loading the blank to measuring the final specifications of the finished part. "Our customers can see that their individual processing process succeeds in the required cycle time and grant the delivery approval as if they were on site."
Other digital tools are also being worked on in the USA. In order to further train the sales partners of the Group and to give them the opportunity to serve their customers even better, virtual sales trainings were also held – with overwhelming success. “Instead of the expected 50 sales partners, 125 took part,” says Joseph Szenay.
Smart Glasses as a Device
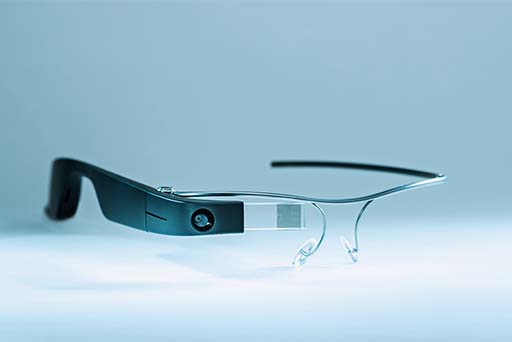
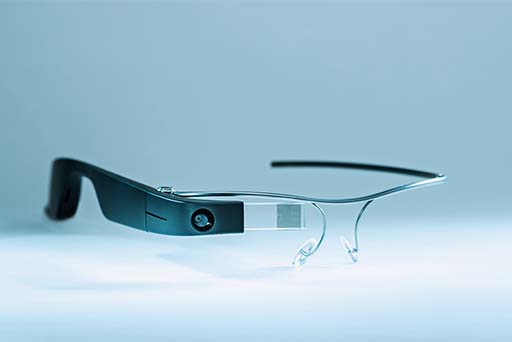
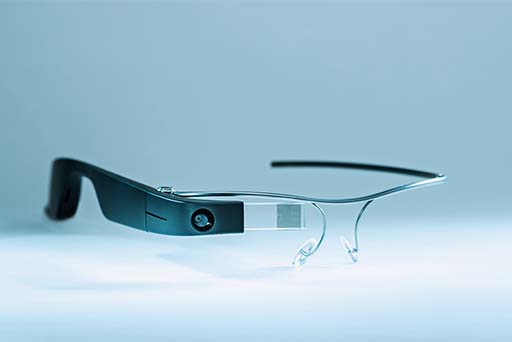
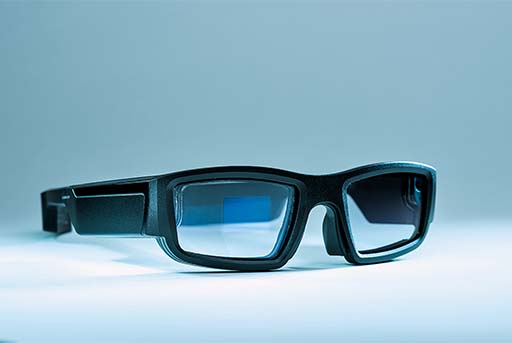
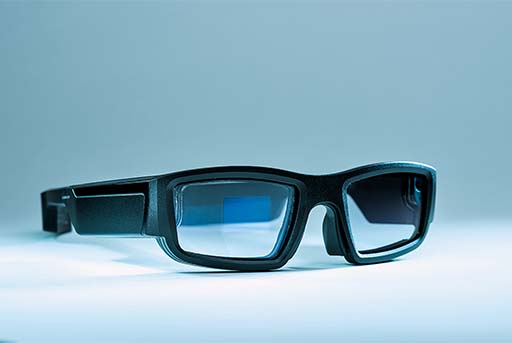
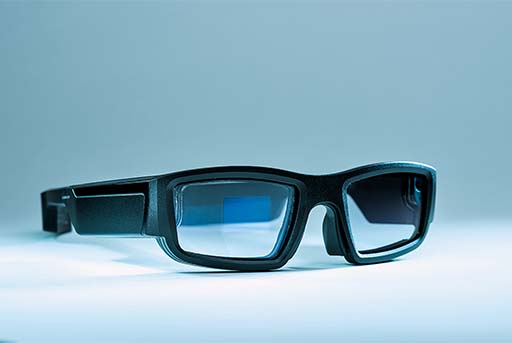
After the integration of smartphone/tablet (mobile devices), the Digital Solutions team is now working on Smart Glasses as a device. “Smart Glasses offer several great opportunities,” emphasizes Head of Digital Engineering Christian Josi. On the one hand, the technicians on the machine have their hands free, and on the other hand, the specialist at the help desk of UNITED GRINDING shares the exact view of their counterpart on the machine – the so-called “See what I see” effect. An additional extension would be contextual information, which can be applied directly to the employee on the machine via augmented reality applications. This is already being tested in Bern.
What interventions can customers perform with help desk support? “This is very different and depends on the customer individually,” Liesenfeld emphasizes. “Some of our customers have fully trained maintenance teams. All they need is machine-specific hints from our help desk.” In addition, many mixed forms are conceivable. “In the case of major repairs, the customer staff, guided by the Remote Service, may already be doing preparatory work and our technician will only do the actual repair.”
Nor does it necessarily have to be about repair and maintenance. “Remote process optimization is also conceivable,” explains CTO Christoph Plüss. In this way, production processes could be optimized using remote technology. Of course, the data from the Production and Service Monitor would also be included in such a process. “This is a full circle of our digital solutions”, says Plüss.