FINO A MARTE
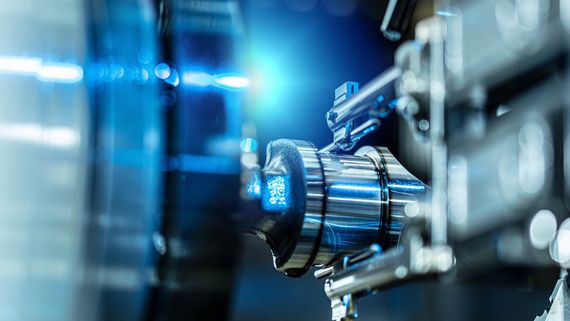
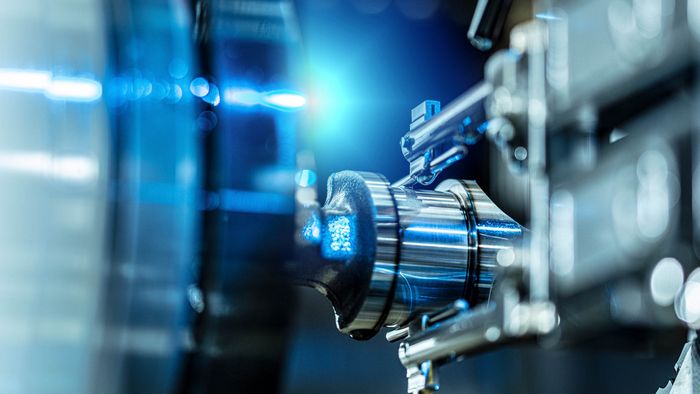
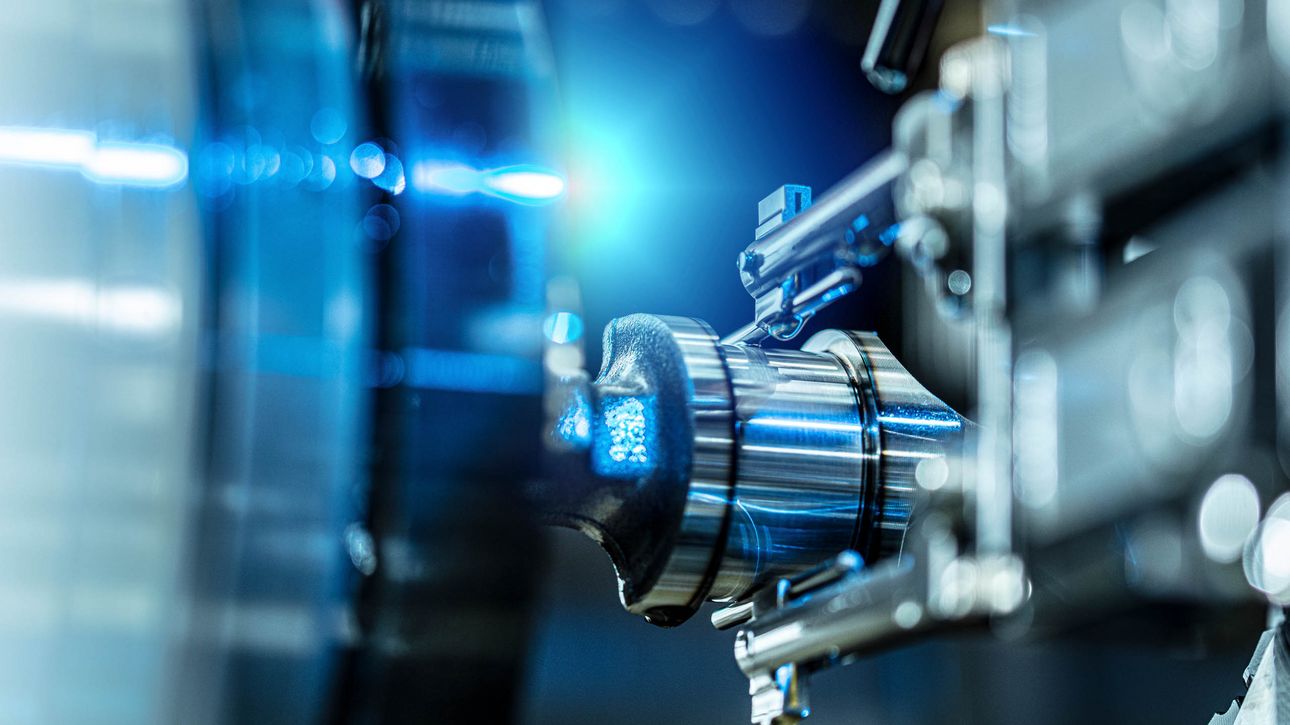
UNA SEMPLICE SCATOLA GRIGIA si erge sulle sabbie rosse di Marte. Dal sistema satellitare sale del fumo. Alexander Gerst controlla il robot Rollin’ Justin da una navicella spaziale. Il robot apre il dispositivo sulla superficie di Marte. Individua il modulo che fuma e lo sostituisce con uno nuovo. Con il tablet l’astronauta programma le operazioni che il robot deve eseguire. Fatto! La comunicazione con il pianeta rosso è assicurata. Certo, era solo una simulazione. Il robot si trovava nel centro spaziale di Oberpfaffenhofen, in Germania, e Alexander Gerst lo ha controllato dalla Stazione Spaziale Internazionale (ISS). I robot intelligenti sono considerati un fattore chiave nella scoperta e nell’esplorazione di pianeti distanti. E forse, con Rollin ‘Justin o con un suo collega, un pezzo di tecnologia di rettifica di UNITED GRINDING Group potrebbe sbarcare anche su Marte. I cosiddetti Robot Speed Reducer Gears sono utilizzati nei giunti articolati dei robot. Questi ingranaggi riducono la velocità del motore che aziona i giunti. Senza di essi, il robot non sarebbe in grado di eseguire movimenti misurati. “La combinazione di economicità, prestazioni e qualità di lavorazione è alla base della superiorità della rettifica rispetto a qualsiasi altro processo di produzione”, spiega il prof. Konrad Wegener dell’Istituto per le macchine utensili e la lavorazione industriale dell’ETH di Zurigo. I Robot Speed Reducer Gears ne sono una chiara dimostrazione: con la rettifica vengono realizzate nei giunti scanalature semicircolari con una tolleranza del diametro di +/- 3 μm. La lavorazione si svolge 24 ore su 24, 7 giorni su 7, senza operatore. “Circa 2,5 milioni di tali ingranaggi vengono rettificati ogni anno con macchine MÄGERLE”, stima il product manager Viktor Ruh.
TRE CRITERI
La rettifica come processo di lavorazione ad asportazione è una tecnica antica. Già nell’antichità greca le pietre usate per levigare venivano raffreddate con acqua o olio. La prima rettificatrice cilindrica ha fatto la sua comparsa sul mercato nel 1845. E nei 174 anni successivi, questo processo di produzione non ha mai perso importanza. “Il processo è oggi in grado di offrire le massime velocità di asportazione, tempi di ciclo brevi e usura minima dell’utensile. Nessun’altra tecnologia è in grado di offrire tanto”, riassume Harri Rein. Rein è CTO del gruppo tecnologico Utensili. Daniel Huber svolge la stessa funzione per il gruppo Rettifica cilindrica e Daniel Mavro per il gruppo Rettifica in piano e di profili. Insieme a Christoph Plüss, Chief Technology Officer del Gruppo, formano il CTO Board che stabilisce le linee guida per lo sviluppo tecnologico degli otto marchi aziendali. La rettifica non è utilizzata solo nella robotica, ma anche nella microelettronica. I cosiddetti wafer, semiconduttori che fungono da base per i componenti elettronici, sono rettificati. Nelle tecnologie innovative, l’uso di nuovi materiali è spesso possibile solo utilizzando specifici processi di lavorazione. I compositi ceramici, utilizzati ad esempio nei propulsori dell’industria aerospaziale, possono essere lavorati al meglio con la rettifica. “I componenti leggeri per il settore automobilistico o aerospaziale, in plastica rinforzata con fibre di carbonio, sono lavorati con utensili in DPC che hanno subito un processo di rettifica”, spiega Huber.
VANTAGGI NELLE APPLICAZIONI
L’elevata qualità di lavorazione della rettifica offre numerosi vantaggi nelle applicazioni industriali. “Le finiture di superficie più fini nel settore automobilistico riducono l’attrito aumentando l’efficienza del motore”, spiega Mavro. “Tolleranze più strette nell’industria aeronautica e aerospaziale aumentano l’efficienza dei propulsori, ad esempio riducendo le perdite di flusso d’aria di raffreddamento.” Nel settore automobilistico, i marchi del Gruppo offrono molte applicazioni innovative. Ad esempio, la rettifica di alberi di equilibratura sulla SCHAUDT ShaftGrind S. Questi riducono la rumorosità del motore a combustione interna generando controfrequenze. Non sono né rettilinei né cilindrici e rappresentano quindi una grande sfida per la lavorazione. Oppure, la lavorazione di cremagliere su una MÄGERLE MFP che può rettificare fino a otto pezzi in una sola operazione di serraggio, con profili di profondità fino a undici millimetri e larghezza fino a 300 millimetri – una sfida estrema in termini di prestazioni del mandrino e stabilità dell’intera macchina.
MISURAZIONE E RETTIFICA
L’effettivo processo di rettifica può associarsi a processi complementari come la misurazione o la ravvivatura. “Una rettificatrice può essere configurata insieme a una misuratrice come “cella” e caricata per mezzo di un robot come interfaccia”, spiega il CTO Rein. Il risultato è una lavorazione senza operatore, detta anche “lights out”, che consente la produzione di grandi quantità di pezzi. Nell’Internal Measuring System (IMS) di WALTER è possibile memorizzare i parametri degli utensili da produrre. In caso di discrepanze, il sistema regola il processo di lavorazione o interrompe la produzione quando si esce dal campo di tolleranza. “Anche con piccoli lotti o singoli pezzi, la misurazione “in process” è importante per ottenere immediatamente l’accuratezza richiesta”, spiega Huber. La ravvivatura compensa l’usura della mola. In questo modo sono garantite esattamente le stesse tolleranze del pezzo e la stessa qualità durante l’intero ciclo di produzione. “In alcune applicazioni, vengono utilizzati materiali sempre più duri, come la ceramica, che richiedono superabrasivi e questi a loro volta necessitano di un agglomerante della mola altamente resistente, vale a dire metallico”, spiega Wegener. E per una mola ad agglomerante metallico, la tecnologia WireDress® è il metodo di elezione per la ravvivatura. Secondo il principio dell’elettroerosione a filo, la mola viene ravvivata senza contatto. Il risultato è la massima sporgenza dei grani e una capacità di taglio ottimale. “Credo che WireDress® incrementerà in modo decisivo l’impiego delle mole ad agglomerante metallico”, dichiara Wegener il cui istituto ha sviluppato la tecnologia in collaborazione con STUDER.
IL FATTORE UMANO
Un altro fondamentale fattore da cui dipende il risultato del processo di rettifica è l’operatore. “La sua esperienza è di grande importanza”, sottolinea il CTO Rein. È per questo che tutte le società di UNITED GRINDING Group investono molte risorse nella formazione professionale dei propri collaboratori (vedere anche pagina 36 e seguenti). Il know-how umano manterrà la sua importanza anche nelle prossime fasi della digitalizzazione. “Da un lato, il know-how degli esperti di rettifica di oggi deve confluire nei sistemi di assistenza e nelle banche dati, dall’altro, in futuro, verranno assegnati all’operatore compiti più impegnativi”, spiega Huber. Quindi: “In una cella di produzione complessa, l’operatore necessita di capacità di un livello diverso”, aggiunge Mavro. E così UNITED GRINDING Group si è posto due obiettivi: tecnologie sempre migliori e collaboratori sempre migliori. Entrambi i fattori concorrono a conseguire risultati di rettifica sempre migliori.